Video here:
http://video.sina.com.cn/news/spj/topvideoes20190411/?opsubject_id=top1#287255705
The made one and used for HK-Macau-Zhuhai submarine tunnel project. Now they build yet another one larger than the 1st.
https://www.chinanews.com/cj/2019/04-09/8804404.shtml
世界最大碎石铺设整平船下水 将建设深中通道沉管隧道
2019年04月09日 21:00 来源:中国新闻网
参与互动
世界最大碎石铺设整平船下水 岳路建 摄
中新网广州4月9日电(蔡敏婕 岳路建)广东省交通集团9日发布消息称,由中国自主研发、目前世界最大的自升平台式碎石铺设整平船“津平2”,在上海振华重工南通制造基地顺利下水,投产后将进一步巩固中国在海底隧道基础施工领域的世界领先地位。
3个月后,“津平2”将航行超过1750公里,漂洋过海至粤港澳大湾区核心工程——深中通道沉管隧道的建设现场,开展沉管基槽碎石整平施工,为今年底深中通道首节沉管安放奠定重要基础。
深中通道沉管隧道长约6.8公里,其中沉管段长约5.035公里,将由32节深埋在伶仃洋海底40多米深基槽内的沉管组成。
世界最大碎石铺设整平船下水 岳路建 摄
“在海底隧道施工过程中,基槽碎石整平是沉管基础质量控制重要环节之一,因此碎石整平船也是沉管隧道质量控制的重要保障设备。”深中通道管理中心副总工程师李进称。
据了解,自升平台式碎石铺设整平船“津平2”是专为深中通道项目研发的专用作业船舶,长98.7米,宽63.3米,其面积相当于一个足球场大小,负责铺设深中通道水深10-35m范围内所有沉管管节的碎石垫层,该船具有石料抛投和高精度整平作业能力,是集定位测量、水下抛石、浅水整平、质量检测功能于一体大型多功能专用装备,也是目前世界上最大的外海施工船舶,也是世界上最先进的先铺法碎石基床整平船。
自去年7月正式开工以来,经过8个月的奋战实现整船下水,并将再用约3个月时间完成后期舾装、设备调试,预计今年7月抵达深中通道现场进行调试。
“‘津平2’的施工管理系统实现了整套系统中国国产化。”该船监造组技术负责人王明亮介绍,施工管理系统相当于船舶的“大脑”,担任施工作业的“总指挥”,发出指令,协调各方同时运行。
据了解,曾用于港珠澳大桥沉管隧道建设的碎石整平船‘津平1’,所采用的施工管理系统由日本建造。在此基础上,造船团队吸取经验,通过自主研发创新,“津平2”在所有铺设施工作业环节实现了全自动化控制、一体化管理,在性能、规格各个方面实现全面超越,多项性能位居国际领先水平,将有效提升深中通道隧道沉管安装的工效和质量。
目前,深中通道桥梁工程已经全线展开,伶仃洋大桥东锚碇已完成围堰筑岛及回填;岛隧工程方面,西人工岛顺利完成筑岛,岛上隧道敞开段开始施工,东人工岛堰筑段隧道围堰工程及成岛施工已展开,沉管隧道预计今年完成E1、E2管节钢壳制造和浇筑。按照计划,依托深中通道工程研制的另一个核心装备、世界第一艘且唯一一艘沉管运输安装一体船计划下半年进行联调联试,为首节沉管安放进行准备。(完)
【编辑:姜贞宇】
https://zhuanlan.zhihu.com/p/29135924
港珠澳大桥海底隧道怎么修?第一步用大船铺“路基”
网易《了不起的中国制造》
已认证的官方帐号
(“津平1号”抛石整平船)
“津平1号”型长81.8米,型宽46米,型深5.5米,设计吃水4米,总重约6500吨,排水量约9800吨,是国产世界上最大的,也是唯一一艘具备清淤功能的平台式深海抛石整平船,2017年3月4日,“津平1号”完成了港珠澳大桥沉管隧道全部33节沉管的碎石基床铺设重任。
(一)抛石整平船是如何工作的?
抛石整平船,顾名思义,其主要工作包括两个部分:其一,向海底抛洒碎石;其二,把碎石弄平,形成海底坚实可靠的基床,以便于海底隧道的铺设。其完成的工作类似于铺设铁轨之前修建碎石枕木路基的过程,只不过施工地点是在海底。
“津平1号”的基本工作过程为:
1.抛石船由拖船拖航到位,经GPS定位后,抛6只定位锚,通过6台定位锚机将船体定位在施工工位上;
2. 桩腿插入海底站稳后,对桩腿施加载荷,以确保施工过程中船体稳固;
3. 预压载完成后,将船体顶升离开水面;
4. 碎石通过石料传送系统从取料漏斗输送到总长达75米的抛石管;
5. 通过大小车的联合移动,带动抛石管在船体中间的“口”字形月池中移动,以完成抛石整平作业;
6. 当一个船位的抛石整平和检查验收作业完成后,下降船体,抬升桩腿,抛石船移到下一个船位,重复抛石整平作业;
7. 重复完成7个船位的抛石整平作业即可铺设完一个标准沉管隧道的碎石垫层。
(抛石整平船结构示意图)
上面的操作流程看起来简单,但其中包含的技术含量却不小。而且由国家知识产权局和世界知识产权组织审核决定,“深水抛石整平船”专利在2015年荣获有“中国知识产权奥斯卡”之称的中国专利奖金奖。
其中到底有哪些门道,今天就带大家进行深入解读。
(二)抛石整平船工作时如何保证船体稳定?
为了实现良好的抛石整平精度,需要很多关键技术,其中最基本的一项要求是保证工作状态下船体的平稳。
1、采用自升式结构,船体稳稳插入海底
“津平1号”采用了自升式结构,工作时将布置在船体四角处的4条90米长的桩腿插入海底,将船体整体提升到海平面以上,以防海浪引起船体晃动。
但是,单纯的插入海底还不够。这就好比将钉子插入土中后,还需要用锤子进行敲打才能使其彻底稳固。
2、预压载系统像锤子一样将桩腿打牢
同样,“津平1号”的桩腿插入海底将平台提升起来之后,平台的重量、可变载荷、风浪流引起的载荷都会加在桩腿上,如果插入海底的桩腿不够牢靠则会继续下陷,影响船体位置固定,在海况恶劣的情况下甚至会发生海床穿透,产生灾难性后果。
因此十分有必要找到一把有效的“锤子”将其打牢,这把锤子就是平台上的预压载系统。
预压载的目的是让桩腿在海床中插得更深,为了实现这样的目的,平台可采用两种压载方式。
第一种是对角线压载:当四根桩腿都插入海床中并将平台提升起来之后,先锁死对位于角线的两条桩腿,然后对另外两条桩腿利用升降装置伸长来施加载荷。当载荷达到一定程度后将桩腿锁死,然后对另外两条进行加载,如此交替进行,直至预加载荷满足要求。这种方式相当于船体平台总重量不变,通过四条支撑变两条支撑的方式来增大压强,实现压载。
另外一种加载方式是四角均衡压载,在4条桩腿都插入泥土中后,通过布置在船舷两侧的4台加载水泵向平台的8个压载水舱内打入压载水,提升船体总重量,利用压载水近万吨的重量,实现均衡压载。在这种压载方式中,要保证各水舱进水速度一致,以保证压载过程中的平衡。
3、桩腿升降系统:失去一个齿轮仍能正常工作
作为整个平台的支撑,桩腿的重要性不言而喻。不仅要把“钉子”打的深,钉子本身也要足够坚固。
桩腿结构需要面临体积大、内部结构复杂、焊接要求高、焊接空间不足等问题。
为此桩腿结构采用钢管外焊接两条背对背安装的齿条形式,通过8组齿轮进行升降驱动,将桩腿设计成一套独立完整的升降系统,便于整体安装和维护。
(桩腿提升系统示意图)
为了进一步保证桩腿提升系统的可靠性,在设计时对升降系统可能发生的故障进行了评估。根据评估结果在桩腿正常工作和加载工作的情况下,若因故障突然失去一个齿轮,升降系统里的其他7个齿轮的负载仍能保证在最大负载的要求之内,不影响正常工作。
(三)抛石整平船如何精确抛石整平?
总长5664米的沉管隧道为节段式设计,共33个管节,标准管节由8个管段组成,长180米、宽37.95米、高11.4米,质量超过72000吨。
(铺设管节截面图)
为这样的管节铺设碎石路基,首先要保证伸入海中的抛石管具有多维空间移动的能力。
为此平台上的移动大车、小车夹持着抛石管在水平面“口”字形范围内移动,随动式皮带则跟随小车移动,保证充足的碎石原料供给,升降绞车则负责抛石管的升降运动。
有了上述装置,抛石系统可以正常运作。但为了实现良好的抛石精度,直径1524毫米的抛石管的头部是固定的主管和可以伸缩的平衡管,通过4套平衡油缸上的4套位移传感器共同作用,可以调节平衡管的伸缩长度,以满足抛石整平的精度要求。
而且抛石管头部还安装有两套声呐系统,用于检测海底槽床和已铺设碎石基层的高度。根据声呐检测的结果,动态调整抛石管位置。
同时平台中还设有两套倾斜管理系统,用来实时检测船体和抛石管的倾斜角度,并根据铺设要求进行相应的矫正。
(四)抛石整平船还能做什么?
在碎石基床完工后,因为存在海底的淤泥重新覆盖基床的风险,沉管隧道也不能保证完全顺利的铺设。
在港珠澳大桥海底隧道的铺设过程中,E22沉管就因台风的影响而遭遇大面积基床回淤,影响后续正常施工。
当时国内外海工作业工程中从未有过在水深48米这样水流环境恶劣的情况下进行高精度、高效率清淤的实践先例可供参考。
进过现场分析和技术评定,最好的解决方案是对现有的“津平1号”进行改造,使之成为具有清淤功能的抛石整平船。“津平1号”利用技术改进后的清淤功能,在28个有效工时内完成2000多平方米的基床高精度清淤,创造了水工行业上一次伟大的技术跨越。
(清淤系统示意图,图中红色框部分)
在“津平1号”抛石整平的基础上,增设了新一套的大小车移动平台及升降塔架将清淤系统的吸头置于铺设好的基床上方,利用清淤泵吸入淤泥并将其提升至平台上。平台上的移动桁架上的排泥管和排泥软管相连,最终淤泥经由排泥软管被排放到1千米之外的海中,消除了对海底铺设好的基床的影响。
碎石基床处于深水,环境复杂,能见度差,清淤系统在进行有效吸入淤泥的同时还不能破坏已经铺设还的碎石,这需要一系列计算后对吸头位置和吸力进行精确控制。为此需要借助强光照明、水下成像设备、声呐多波束扫描成像等手段获取碎石基床状态数据,保障清淤工作的顺利实施。
结语:
“津平1号”自升式抛石整平平台作为港珠澳大桥岛隧工程的重要装备,对中国海工领域的高精度抛石整平平台的设计和建造具有重要的意义。
相比于普通抛石整平船,该平台除体积和工作范围更大之外,还能同时完成抛石、整平、清淤等多项作业,且拥有良好的平整度,填补了中国在这一领域的空白,为中国建设世界级跨海大桥等高难度海上工程提供了有效的助力。
作为世界上认知度最高的标签,中国制造(Made in China)正寻求战略升级。「了不起的中国制造」专栏,力邀行业权威、资深玩家,呈现他们眼中的中国创新之路。
投稿请联系[email protected],稿件一经刊用,将提供千字800元的稿酬。
--------------------
编辑| 史文慧
发布于 2017-09-07
The world's largest gravel laying flattening ship launching will construct a deep-medium tunnel immersed tunnel
April 09, 2019 21:00 Source: China News Network Participation
The world's largest gravel laying and leveling ship launching will construct a deep-medium tunnel immersed tunnel
The world's largest gravel laying flat boat launching
Zhongxin.com, Guangzhou, April 9 (Cai Min, Yu Yue Road) Guangdong Communications Group announced on the 9th that China's independent research and development, the world's largest self-elevating platform-type gravel laying flattening ship "Jinping 2", in Shanghai Zhenhua Heavy Industry Nantong Manufacturing Base has been successfully launched, and will further consolidate China's world leading position in the basic construction of subsea tunnels.
After 3 months, “Jinping 2” will sail more than 1,750 kilometers, drifting across the sea to the construction site of the deep tunnel immersed tunnel in the core project of Guangdong, Hong Kong and Macao Dawan District, and carry out the construction of the sinking foundation gravel leveling. To lay an important foundation for the first section of the immersed tube in the deep middle of the channel this year.
The deep-medium immersed tunnel is about 6.8 kilometers long, and the immersed section is about 5.035 kilometers long. It will consist of 32 immersed pipes buried deep in the deep base of the Bohai Sea at more than 40 meters.
The world's largest gravel laying flat boat launching
The world's largest gravel laying flat boat launching
"In the construction process of submarine tunnels, the foundation gravel leveling is one of the important links in the quality control of the immersed pipe foundation. Therefore, the gravel leveling ship is also an important guarantee device for the quality control of the immersed pipe tunnel." Vice President of the Deep Central Channel Management Center Engineer Li Jin said.
It is understood that the self-elevating platform-type gravel laying and leveling ship "Jinping 2" is a special-purpose working ship specially developed for the Shenzhong Channel project. It is 98.7 meters long and 63.3 meters wide. Its area is equivalent to the size of a football field and is responsible for laying deep. The gravel cushion of all immersed pipe joints in the water depth range of 10-35m, the ship has the ability of stone throwing and high-precision leveling operation. It is a set of positioning measurement, underwater riprap, shallow water leveling and quality inspection function. One large-scale multi-purpose special equipment is also the largest offshore construction ship in the world, and it is also the world's most advanced first-stage gravel bed leveling ship.
Since the official start of construction in July last year, after 8 months of hard work, the entire ship will be launched, and it will take about 3 months to complete the post-assembly and equipment commissioning. It is expected to arrive at the Shenzhen-Shenzhen channel for commissioning in July this year.
“The construction management system of 'Jinping 2' has realized the localization of the whole system in China.” Wang Mingliang, technical director of the ship supervision team, introduced that the construction management system is equivalent to the “brain” of the ship and served as the “general commander” of the construction operation. The instructions coordinate the parties to run simultaneously.
It is understood that the construction management system used for the crushed stone leveling ship 'Jinping 1' used in the construction of the immersed tunnel of the Hong Kong-Zhuhai-Macao Bridge was built in Japan. On this basis, the shipbuilding team draws on the experience and through independent research and development and innovation, “Jinping 2” realizes full automation control and integrated management in all laying construction operations, achieving comprehensive transcendence in performance and specifications, and many performances are in place. The international leading level will effectively improve the ergonomics and quality of the immersed pipe installation in the tunnel.
At present, the deep-channel bridge project has been launched. The east anchorage of the Lingyang Bridge has completed the island construction and backfilling. In the island tunnel project, the west artificial island successfully completed the island construction, and the open section of the island tunnel began construction. The tunnel construction of the island and the construction of the island have been started. The immersed tunnel is expected to complete the manufacture and pouring of the E1 and E2 pipe sections this year. According to the plan, another core equipment developed by the Shenzhong Passage Project, the world's first and only one immersed pipe transport and installation integrated ship plan will be jointly tested in the second half of the year to prepare for the first immersed pipe placement. (Finish)
[Editor: Jiang Yuyu]
Https://zhuanlan.zhihu.com/p/29135924
How to repair the Hong Kong-Zhuhai-Macao Bridge Cross-Harbour Tunnel? The first step is to repair the "subgrade" of the Hong Kong-Zhuhai-Macao Bridge under the large ship. The first step is to use the big ship to "subgrade".
NetEase "Great China Made"
NetEase "Great China Made"
Certified official account
Produced | Netease News College
Author | Wang Ze, Ph.D., Department of Mechanical Engineering, Tsinghua University
The Hong Kong-Zhuhai-Macao Bridge, which was built in Guangdong, Hong Kong and Macao, will become the longest sea-crossing bridge in the world. Its main structure, the submarine immersed tunnel, is 5,664 meters long and is the longest immersed tunnel in the world. There is a big difference between laying a subsea tunnel and building a tunnel on land. In order to avoid the impact of unstable silt on the tunnel, it is necessary to first lay a bed on the seabed with gravel and then lay a immersed tunnel on the bed. To complete the gravel bed laying task is today's protagonist - "Jinping No. 1" riprap flattening ship.
("Jinping No. 1" riprap flattening ship)
“Jinping No.1” is 81.8 meters long, 46 meters wide and 5.5 meters deep. It has a design draft of 4 meters, a total weight of about 6,500 tons, and a displacement of about 9,800 tons. It is the largest and only one in the world. The platform-type deep-sea riprap leveling ship with silting function, on March 4, 2017, “Jinping No. 1” completed the heavy stone bed laying of all 33 immersed pipes of the Hong Kong-Zhuhai-Macao Bridge immersed tunnel.
(1) How does the riprap flattening work?
The riprap flattening ship, as its name suggests, consists of two parts: one, throwing gravel to the seabed; and the other, flattening the gravel to form a solid and reliable bed on the seabed to facilitate the laying of the subsea tunnel. The work done is similar to the process of building a gravel sleeper roadbed before laying rails, except that the construction site is on the sea floor.
The basic working process of “Jinping No. 1” is:
1. The riprap boat is towed by the tugboat. After GPS positioning, 6 anchors are towed, and the hull is positioned at the construction station through 6 positioning anchors;
2. After the pile legs are inserted into the seabed and stabilized, a load is applied to the pile legs to ensure the hull is stable during the construction process;
3. After the pre-ballast is completed, the hull is lifted off the water surface;
4. The gravel is transported from the reclaiming funnel through a stone conveying system to a riprap pipe with a total length of up to 75 m;
5. Through the joint movement of large and small cars, the riprap pipe is moved in the “mouth” shaped moon pool in the middle of the hull to complete the riprap leveling operation;
6. When the riprap leveling and inspection and acceptance work of one position is completed, the hull is lowered, the pile legs are lifted, the riprap boat is moved to the next position, and the riprap leveling operation is repeated;
7. Repeat the completion of the riprap leveling operation of 7 positions to lay the gravel cushion of a standard immersed tunnel.
(Splash diagram of riprap flattening ship)
The above process seems simple, but the technical content contained in it is not small. Moreover, the State Intellectual Property Office and the World Intellectual Property Organization reviewed and decided that the “Deepwater Riprap Flattening Ship” patent won the China Patent Prize in 2015, which is known as “China Intellectual Property Oscar”.
In the end, what are the doorways, and today we will take you to an in-depth interpretation.
(2) How to ensure the stability of the hull when the riprap is leveled?
In order to achieve good riprap leveling accuracy, many key technologies are required. One of the most basic requirements is to ensure the smoothness of the hull under working conditions.
1. Adopting self-lifting structure, the hull is stably inserted into the seabed
"Jinping No. 1" adopts a self-elevating structure. During work, four 90-meter-long legs placed at the four corners of the hull are inserted into the seabed to lift the hull as a whole above sea level to prevent the hull from swaying.
However, simply inserting the bottom of the sea is not enough. This is like inserting a nail into the soil and hitting it with a hammer to make it completely stable.
2. The pre-ballast system will fasten the legs like a hammer.
Similarly, after the legs of “Jinping No. 1” are inserted into the sea floor to lift the platform, the weight caused by the weight of the platform, the variable load, and the load caused by the wind and waves will be added to the pile legs. If the legs inserted into the sea floor are not secure enough, the pile will continue to sink. , affecting the fixed position of the hull, even in the case of poor sea conditions, seabed penetration may occur, with catastrophic consequences.
Therefore, it is very necessary to find an effective "hammer" to fasten it. This hammer is the pre-ballast system on the platform.
The purpose of pre-ballasting is to allow the legs to be inserted deeper into the seabed. To achieve this, the platform can be used in two ballasting modes.
The first type is diagonal ballast: when the four legs are inserted into the seabed and the platform is lifted, the two legs at the corner are locked first, and then the lifting device is used for the other two legs. Stretch to apply a load. When the load reaches a certain level, the leg is locked, and then the other two are loaded, so alternately until the preload is satisfactory. This method is equivalent to the total weight of the hull platform, and the pressure is increased by means of four supports and two supports to achieve ballast.
The other loading method is four-corner balanced ballast. After the four legs are inserted into the soil, the ballast water is pumped into the eight ballast tanks of the platform through four loading pumps arranged on both sides of the ship's side. The total weight of the hull, using the weight of ballast water of nearly 10,000 tons, to achieve balanced ballast. In this ballast mode, it is necessary to ensure that the water inlet speeds of the water tanks are consistent to ensure the balance during the ballasting process.
3, pile leg lifting system: losing a gear can still work normally
As the support of the entire platform, the importance of the legs is self-evident. Not only must the "nails" be deep, but the nails themselves must be strong enough.
The pile leg structure needs to face problems such as large volume, complicated internal structure, high welding requirements, and insufficient welding space.
For this purpose, the leg structure is welded by two steel pipes and back-to-back. The eight legs are used for lifting and driving, and the pile legs are designed as an independent and complete lifting system, which is convenient for overall installation and maintenance.
(Spread of the leg lift system)
In order to further ensure the reliability of the leg lifting system, the failure of the lifting system may be evaluated during design. According to the evaluation results, if the leg is in normal working condition and loading work, if the gear suddenly loses a gear due to the fault, the load of the other 7 gears in the lifting system can still be guaranteed within the maximum load requirement and does not affect the normal operation.
(3) How to accurately rip the stone to level the ship?
The immersed tunnel with a total length of 5664 meters is a segmental design with a total of 33 pipe joints. The standard pipe joint consists of 8 pipe segments, 180 meters long, 37.95 meters wide and 11.4 meters high, with a mass of over 72,000 tons.
(laying pipe section sectional view)
To lay a gravel roadbed for such a pipe joint, it is first necessary to ensure that the riprap pipe that protrudes into the sea has the ability to move in a multi-dimensional space.
For this purpose, the mobile cart and trolley on the platform hold the riprap pipe to move within the “mouth” shape of the horizontal plane, and the follower belt follows the trolley to ensure sufficient supply of gravel material. The lifting winch is responsible for the riprap. Lifting movement.
With the above device, the riprap system can operate normally. However, in order to achieve good riprap accuracy, the head of the 1524 mm diameter riprap pipe is a fixed main pipe and a telescopic balance pipe. The four sets of displacement sensors on the four balance cylinders work together to adjust the expansion and contraction of the balance pipe. Length to meet the accuracy requirements of riprap leveling.
Moreover, two sets of sonar systems are installed in the head of the riprap pipe to detect the height of the submarine trough bed and the laid gravel base. The position of the riprap tube is dynamically adjusted based on the results of the sonar detection.
At the same time, there are two sets of tilt management systems in the platform to detect the inclination angle of the hull and the riprap in real time, and correct it according to the laying requirements.
(4) What else can the riprap ship be able to level?
After the completion of the gravel bed, the immersed tunnel cannot guarantee a completely smooth laying because of the risk of re-covering the bed by the m&d on the seabed.
During the laying of the Hong Kong-Zhuhai-Macao Bridge submarine tunnel, the E22 immersed tube was subjected to large-area bed back siltation due to the influence of the typhoon, which affected subsequent normal construction.
At that time, there were never precedents for high-precision and high-efficiency dredging in the sea and work industry projects at home and abroad for the high-precision and high-efficiency dredging in the case of a water depth of 48 meters.
After the on-site analysis and technical assessment, the best solution is to transform the existing “Jinping No.1” into a riprap leveling ship with dredging function. “Jinping No.1” used the improved dredging function of the technology to complete the high-precision dredging of more than 2,000 square meters of bed in 28 effective working hours, creating a great technological leap in the hydraulic industry.
(The schematic diagram of the dredging system, the red box in the figure)
On the basis of the “Jinping No.1” riprap leveling, a new set of large and small mobile platform and lifting tower was added to place the suction head of the dredging system on the laid bed, and the dredging pump was used to suck in the sludge. And promote it to the platform. The m&d pipe on the mobile truss on the platform is connected to the m&d hose, and finally the sludge is discharged into the sea 1 km away via the m&d hose, eliminating the impact on the seabed laid bed.
The gravel bed is in deep water, the environment is complex, and the visibility is poor. The dredging system can effectively inhale the sludge without destroying the already laid gravel. This requires a series of calculations to accurately control the position and suction of the tip. To this end, it is necessary to obtain the status data of the gravel bed by means of strong light illumination, underwater imaging equipment, sonar multi-beam scanning imaging, etc., to ensure the smooth implementation of dredging work.
Conclusion:
The “Jinping No.1” self-elevating riprap leveling platform is an important equipment for the island tunnel project of the Hong Kong-Zhuhai-Macao Bridge. It is of great significance for the design and construction of a high-precision riprap leveling platform in China's offshore industry.
Compared with the ordinary riprap leveling ship, the platform can complete many operations such as riprap, leveling and dredging at the same time, and has good flatness, which fills the gap in China. The gap in this field has provided effective support for China's construction of world-class sea-crossing bridges and other difficult offshore projects.
As the most recognized label in the world, Made in China is seeking a strategic upgrade. The "Great China Made" column invites industry authorities and experienced players to present the road to innovation in China.
Please submit news to [email protected]. Once the manuscript is published, it will provide a reward of 800 yuan.
--------------------
Edit | Shi Wenhui
Published on 2017-09-07
http://video.sina.com.cn/news/spj/topvideoes20190411/?opsubject_id=top1#287255705
The made one and used for HK-Macau-Zhuhai submarine tunnel project. Now they build yet another one larger than the 1st.
https://www.chinanews.com/cj/2019/04-09/8804404.shtml
世界最大碎石铺设整平船下水 将建设深中通道沉管隧道
2019年04月09日 21:00 来源:中国新闻网

世界最大碎石铺设整平船下水 岳路建 摄
中新网广州4月9日电(蔡敏婕 岳路建)广东省交通集团9日发布消息称,由中国自主研发、目前世界最大的自升平台式碎石铺设整平船“津平2”,在上海振华重工南通制造基地顺利下水,投产后将进一步巩固中国在海底隧道基础施工领域的世界领先地位。
3个月后,“津平2”将航行超过1750公里,漂洋过海至粤港澳大湾区核心工程——深中通道沉管隧道的建设现场,开展沉管基槽碎石整平施工,为今年底深中通道首节沉管安放奠定重要基础。
深中通道沉管隧道长约6.8公里,其中沉管段长约5.035公里,将由32节深埋在伶仃洋海底40多米深基槽内的沉管组成。
世界最大碎石铺设整平船下水 岳路建 摄
“在海底隧道施工过程中,基槽碎石整平是沉管基础质量控制重要环节之一,因此碎石整平船也是沉管隧道质量控制的重要保障设备。”深中通道管理中心副总工程师李进称。
据了解,自升平台式碎石铺设整平船“津平2”是专为深中通道项目研发的专用作业船舶,长98.7米,宽63.3米,其面积相当于一个足球场大小,负责铺设深中通道水深10-35m范围内所有沉管管节的碎石垫层,该船具有石料抛投和高精度整平作业能力,是集定位测量、水下抛石、浅水整平、质量检测功能于一体大型多功能专用装备,也是目前世界上最大的外海施工船舶,也是世界上最先进的先铺法碎石基床整平船。
自去年7月正式开工以来,经过8个月的奋战实现整船下水,并将再用约3个月时间完成后期舾装、设备调试,预计今年7月抵达深中通道现场进行调试。
“‘津平2’的施工管理系统实现了整套系统中国国产化。”该船监造组技术负责人王明亮介绍,施工管理系统相当于船舶的“大脑”,担任施工作业的“总指挥”,发出指令,协调各方同时运行。
据了解,曾用于港珠澳大桥沉管隧道建设的碎石整平船‘津平1’,所采用的施工管理系统由日本建造。在此基础上,造船团队吸取经验,通过自主研发创新,“津平2”在所有铺设施工作业环节实现了全自动化控制、一体化管理,在性能、规格各个方面实现全面超越,多项性能位居国际领先水平,将有效提升深中通道隧道沉管安装的工效和质量。
目前,深中通道桥梁工程已经全线展开,伶仃洋大桥东锚碇已完成围堰筑岛及回填;岛隧工程方面,西人工岛顺利完成筑岛,岛上隧道敞开段开始施工,东人工岛堰筑段隧道围堰工程及成岛施工已展开,沉管隧道预计今年完成E1、E2管节钢壳制造和浇筑。按照计划,依托深中通道工程研制的另一个核心装备、世界第一艘且唯一一艘沉管运输安装一体船计划下半年进行联调联试,为首节沉管安放进行准备。(完)
【编辑:姜贞宇】
https://zhuanlan.zhihu.com/p/29135924
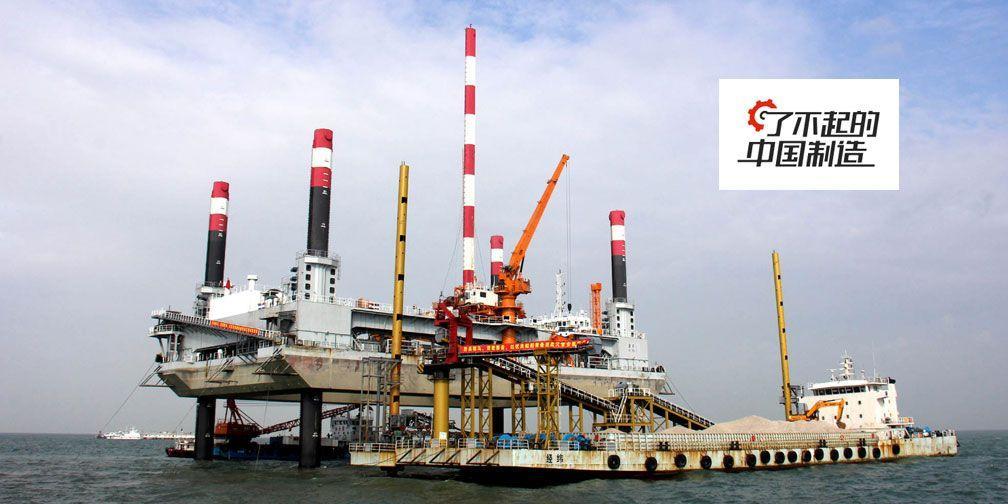
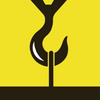
网易《了不起的中国制造》
已认证的官方帐号
出品| 网易新闻学院
作者| 汪泽,清华大学机械工程系博士研究生
粤港澳三地共建的港珠澳大桥建成通车后将成为世界上最长的跨海大桥,其主体结构——海底沉管隧道长5664米,为目前世界上最长的沉管隧道。铺设海底隧道和在陆地上建隧道有很大的不同,为了避免海底不稳定的淤泥对于隧道铺设的影响,需要先在海底用碎石铺设基床,然后再在基床上铺设沉管隧道,而完成碎石基床铺设任务的就是今天的主角——“津平1号”抛石整平船。作者| 汪泽,清华大学机械工程系博士研究生
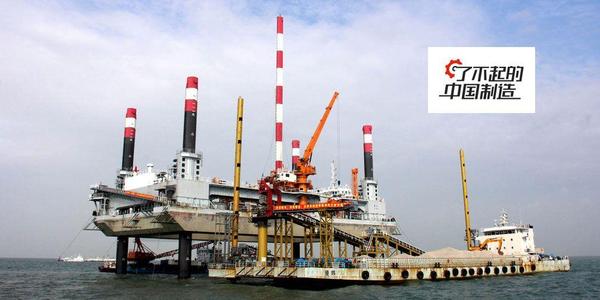
(“津平1号”抛石整平船)
“津平1号”型长81.8米,型宽46米,型深5.5米,设计吃水4米,总重约6500吨,排水量约9800吨,是国产世界上最大的,也是唯一一艘具备清淤功能的平台式深海抛石整平船,2017年3月4日,“津平1号”完成了港珠澳大桥沉管隧道全部33节沉管的碎石基床铺设重任。
(一)抛石整平船是如何工作的?
抛石整平船,顾名思义,其主要工作包括两个部分:其一,向海底抛洒碎石;其二,把碎石弄平,形成海底坚实可靠的基床,以便于海底隧道的铺设。其完成的工作类似于铺设铁轨之前修建碎石枕木路基的过程,只不过施工地点是在海底。
“津平1号”的基本工作过程为:
1.抛石船由拖船拖航到位,经GPS定位后,抛6只定位锚,通过6台定位锚机将船体定位在施工工位上;
2. 桩腿插入海底站稳后,对桩腿施加载荷,以确保施工过程中船体稳固;
3. 预压载完成后,将船体顶升离开水面;
4. 碎石通过石料传送系统从取料漏斗输送到总长达75米的抛石管;
5. 通过大小车的联合移动,带动抛石管在船体中间的“口”字形月池中移动,以完成抛石整平作业;
6. 当一个船位的抛石整平和检查验收作业完成后,下降船体,抬升桩腿,抛石船移到下一个船位,重复抛石整平作业;
7. 重复完成7个船位的抛石整平作业即可铺设完一个标准沉管隧道的碎石垫层。
(抛石整平船结构示意图)
上面的操作流程看起来简单,但其中包含的技术含量却不小。而且由国家知识产权局和世界知识产权组织审核决定,“深水抛石整平船”专利在2015年荣获有“中国知识产权奥斯卡”之称的中国专利奖金奖。
其中到底有哪些门道,今天就带大家进行深入解读。
(二)抛石整平船工作时如何保证船体稳定?
为了实现良好的抛石整平精度,需要很多关键技术,其中最基本的一项要求是保证工作状态下船体的平稳。
1、采用自升式结构,船体稳稳插入海底
“津平1号”采用了自升式结构,工作时将布置在船体四角处的4条90米长的桩腿插入海底,将船体整体提升到海平面以上,以防海浪引起船体晃动。
但是,单纯的插入海底还不够。这就好比将钉子插入土中后,还需要用锤子进行敲打才能使其彻底稳固。
2、预压载系统像锤子一样将桩腿打牢
同样,“津平1号”的桩腿插入海底将平台提升起来之后,平台的重量、可变载荷、风浪流引起的载荷都会加在桩腿上,如果插入海底的桩腿不够牢靠则会继续下陷,影响船体位置固定,在海况恶劣的情况下甚至会发生海床穿透,产生灾难性后果。
因此十分有必要找到一把有效的“锤子”将其打牢,这把锤子就是平台上的预压载系统。
预压载的目的是让桩腿在海床中插得更深,为了实现这样的目的,平台可采用两种压载方式。
第一种是对角线压载:当四根桩腿都插入海床中并将平台提升起来之后,先锁死对位于角线的两条桩腿,然后对另外两条桩腿利用升降装置伸长来施加载荷。当载荷达到一定程度后将桩腿锁死,然后对另外两条进行加载,如此交替进行,直至预加载荷满足要求。这种方式相当于船体平台总重量不变,通过四条支撑变两条支撑的方式来增大压强,实现压载。
另外一种加载方式是四角均衡压载,在4条桩腿都插入泥土中后,通过布置在船舷两侧的4台加载水泵向平台的8个压载水舱内打入压载水,提升船体总重量,利用压载水近万吨的重量,实现均衡压载。在这种压载方式中,要保证各水舱进水速度一致,以保证压载过程中的平衡。
3、桩腿升降系统:失去一个齿轮仍能正常工作
作为整个平台的支撑,桩腿的重要性不言而喻。不仅要把“钉子”打的深,钉子本身也要足够坚固。
桩腿结构需要面临体积大、内部结构复杂、焊接要求高、焊接空间不足等问题。
为此桩腿结构采用钢管外焊接两条背对背安装的齿条形式,通过8组齿轮进行升降驱动,将桩腿设计成一套独立完整的升降系统,便于整体安装和维护。
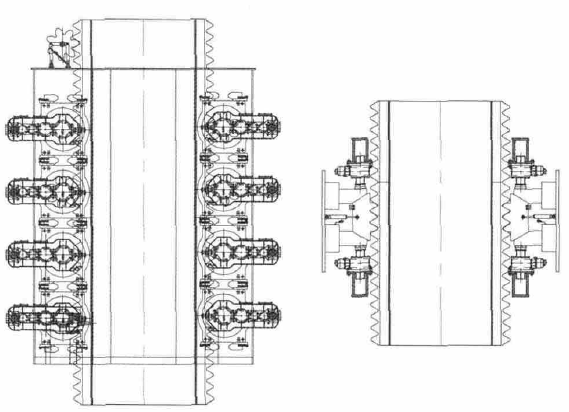
(桩腿提升系统示意图)
为了进一步保证桩腿提升系统的可靠性,在设计时对升降系统可能发生的故障进行了评估。根据评估结果在桩腿正常工作和加载工作的情况下,若因故障突然失去一个齿轮,升降系统里的其他7个齿轮的负载仍能保证在最大负载的要求之内,不影响正常工作。
(三)抛石整平船如何精确抛石整平?
总长5664米的沉管隧道为节段式设计,共33个管节,标准管节由8个管段组成,长180米、宽37.95米、高11.4米,质量超过72000吨。
(铺设管节截面图)
为这样的管节铺设碎石路基,首先要保证伸入海中的抛石管具有多维空间移动的能力。
为此平台上的移动大车、小车夹持着抛石管在水平面“口”字形范围内移动,随动式皮带则跟随小车移动,保证充足的碎石原料供给,升降绞车则负责抛石管的升降运动。
有了上述装置,抛石系统可以正常运作。但为了实现良好的抛石精度,直径1524毫米的抛石管的头部是固定的主管和可以伸缩的平衡管,通过4套平衡油缸上的4套位移传感器共同作用,可以调节平衡管的伸缩长度,以满足抛石整平的精度要求。
而且抛石管头部还安装有两套声呐系统,用于检测海底槽床和已铺设碎石基层的高度。根据声呐检测的结果,动态调整抛石管位置。
同时平台中还设有两套倾斜管理系统,用来实时检测船体和抛石管的倾斜角度,并根据铺设要求进行相应的矫正。
(四)抛石整平船还能做什么?
在碎石基床完工后,因为存在海底的淤泥重新覆盖基床的风险,沉管隧道也不能保证完全顺利的铺设。
在港珠澳大桥海底隧道的铺设过程中,E22沉管就因台风的影响而遭遇大面积基床回淤,影响后续正常施工。
当时国内外海工作业工程中从未有过在水深48米这样水流环境恶劣的情况下进行高精度、高效率清淤的实践先例可供参考。
进过现场分析和技术评定,最好的解决方案是对现有的“津平1号”进行改造,使之成为具有清淤功能的抛石整平船。“津平1号”利用技术改进后的清淤功能,在28个有效工时内完成2000多平方米的基床高精度清淤,创造了水工行业上一次伟大的技术跨越。
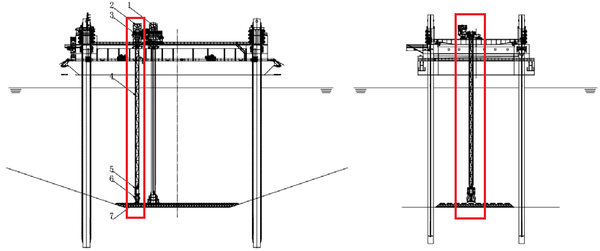
(清淤系统示意图,图中红色框部分)
在“津平1号”抛石整平的基础上,增设了新一套的大小车移动平台及升降塔架将清淤系统的吸头置于铺设好的基床上方,利用清淤泵吸入淤泥并将其提升至平台上。平台上的移动桁架上的排泥管和排泥软管相连,最终淤泥经由排泥软管被排放到1千米之外的海中,消除了对海底铺设好的基床的影响。
碎石基床处于深水,环境复杂,能见度差,清淤系统在进行有效吸入淤泥的同时还不能破坏已经铺设还的碎石,这需要一系列计算后对吸头位置和吸力进行精确控制。为此需要借助强光照明、水下成像设备、声呐多波束扫描成像等手段获取碎石基床状态数据,保障清淤工作的顺利实施。
结语:
“津平1号”自升式抛石整平平台作为港珠澳大桥岛隧工程的重要装备,对中国海工领域的高精度抛石整平平台的设计和建造具有重要的意义。
相比于普通抛石整平船,该平台除体积和工作范围更大之外,还能同时完成抛石、整平、清淤等多项作业,且拥有良好的平整度,填补了中国在这一领域的空白,为中国建设世界级跨海大桥等高难度海上工程提供了有效的助力。
作为世界上认知度最高的标签,中国制造(Made in China)正寻求战略升级。「了不起的中国制造」专栏,力邀行业权威、资深玩家,呈现他们眼中的中国创新之路。
投稿请联系[email protected],稿件一经刊用,将提供千字800元的稿酬。
--------------------
编辑| 史文慧
发布于 2017-09-07
The world's largest gravel laying flattening ship launching will construct a deep-medium tunnel immersed tunnel
April 09, 2019 21:00 Source: China News Network Participation
The world's largest gravel laying and leveling ship launching will construct a deep-medium tunnel immersed tunnel
The world's largest gravel laying flat boat launching
Zhongxin.com, Guangzhou, April 9 (Cai Min, Yu Yue Road) Guangdong Communications Group announced on the 9th that China's independent research and development, the world's largest self-elevating platform-type gravel laying flattening ship "Jinping 2", in Shanghai Zhenhua Heavy Industry Nantong Manufacturing Base has been successfully launched, and will further consolidate China's world leading position in the basic construction of subsea tunnels.
After 3 months, “Jinping 2” will sail more than 1,750 kilometers, drifting across the sea to the construction site of the deep tunnel immersed tunnel in the core project of Guangdong, Hong Kong and Macao Dawan District, and carry out the construction of the sinking foundation gravel leveling. To lay an important foundation for the first section of the immersed tube in the deep middle of the channel this year.
The deep-medium immersed tunnel is about 6.8 kilometers long, and the immersed section is about 5.035 kilometers long. It will consist of 32 immersed pipes buried deep in the deep base of the Bohai Sea at more than 40 meters.
The world's largest gravel laying flat boat launching
The world's largest gravel laying flat boat launching
"In the construction process of submarine tunnels, the foundation gravel leveling is one of the important links in the quality control of the immersed pipe foundation. Therefore, the gravel leveling ship is also an important guarantee device for the quality control of the immersed pipe tunnel." Vice President of the Deep Central Channel Management Center Engineer Li Jin said.
It is understood that the self-elevating platform-type gravel laying and leveling ship "Jinping 2" is a special-purpose working ship specially developed for the Shenzhong Channel project. It is 98.7 meters long and 63.3 meters wide. Its area is equivalent to the size of a football field and is responsible for laying deep. The gravel cushion of all immersed pipe joints in the water depth range of 10-35m, the ship has the ability of stone throwing and high-precision leveling operation. It is a set of positioning measurement, underwater riprap, shallow water leveling and quality inspection function. One large-scale multi-purpose special equipment is also the largest offshore construction ship in the world, and it is also the world's most advanced first-stage gravel bed leveling ship.
Since the official start of construction in July last year, after 8 months of hard work, the entire ship will be launched, and it will take about 3 months to complete the post-assembly and equipment commissioning. It is expected to arrive at the Shenzhen-Shenzhen channel for commissioning in July this year.
“The construction management system of 'Jinping 2' has realized the localization of the whole system in China.” Wang Mingliang, technical director of the ship supervision team, introduced that the construction management system is equivalent to the “brain” of the ship and served as the “general commander” of the construction operation. The instructions coordinate the parties to run simultaneously.
It is understood that the construction management system used for the crushed stone leveling ship 'Jinping 1' used in the construction of the immersed tunnel of the Hong Kong-Zhuhai-Macao Bridge was built in Japan. On this basis, the shipbuilding team draws on the experience and through independent research and development and innovation, “Jinping 2” realizes full automation control and integrated management in all laying construction operations, achieving comprehensive transcendence in performance and specifications, and many performances are in place. The international leading level will effectively improve the ergonomics and quality of the immersed pipe installation in the tunnel.
At present, the deep-channel bridge project has been launched. The east anchorage of the Lingyang Bridge has completed the island construction and backfilling. In the island tunnel project, the west artificial island successfully completed the island construction, and the open section of the island tunnel began construction. The tunnel construction of the island and the construction of the island have been started. The immersed tunnel is expected to complete the manufacture and pouring of the E1 and E2 pipe sections this year. According to the plan, another core equipment developed by the Shenzhong Passage Project, the world's first and only one immersed pipe transport and installation integrated ship plan will be jointly tested in the second half of the year to prepare for the first immersed pipe placement. (Finish)
[Editor: Jiang Yuyu]
Https://zhuanlan.zhihu.com/p/29135924
How to repair the Hong Kong-Zhuhai-Macao Bridge Cross-Harbour Tunnel? The first step is to repair the "subgrade" of the Hong Kong-Zhuhai-Macao Bridge under the large ship. The first step is to use the big ship to "subgrade".
NetEase "Great China Made"
NetEase "Great China Made"
Certified official account
Produced | Netease News College
Author | Wang Ze, Ph.D., Department of Mechanical Engineering, Tsinghua University
The Hong Kong-Zhuhai-Macao Bridge, which was built in Guangdong, Hong Kong and Macao, will become the longest sea-crossing bridge in the world. Its main structure, the submarine immersed tunnel, is 5,664 meters long and is the longest immersed tunnel in the world. There is a big difference between laying a subsea tunnel and building a tunnel on land. In order to avoid the impact of unstable silt on the tunnel, it is necessary to first lay a bed on the seabed with gravel and then lay a immersed tunnel on the bed. To complete the gravel bed laying task is today's protagonist - "Jinping No. 1" riprap flattening ship.
("Jinping No. 1" riprap flattening ship)
“Jinping No.1” is 81.8 meters long, 46 meters wide and 5.5 meters deep. It has a design draft of 4 meters, a total weight of about 6,500 tons, and a displacement of about 9,800 tons. It is the largest and only one in the world. The platform-type deep-sea riprap leveling ship with silting function, on March 4, 2017, “Jinping No. 1” completed the heavy stone bed laying of all 33 immersed pipes of the Hong Kong-Zhuhai-Macao Bridge immersed tunnel.
(1) How does the riprap flattening work?
The riprap flattening ship, as its name suggests, consists of two parts: one, throwing gravel to the seabed; and the other, flattening the gravel to form a solid and reliable bed on the seabed to facilitate the laying of the subsea tunnel. The work done is similar to the process of building a gravel sleeper roadbed before laying rails, except that the construction site is on the sea floor.
The basic working process of “Jinping No. 1” is:
1. The riprap boat is towed by the tugboat. After GPS positioning, 6 anchors are towed, and the hull is positioned at the construction station through 6 positioning anchors;
2. After the pile legs are inserted into the seabed and stabilized, a load is applied to the pile legs to ensure the hull is stable during the construction process;
3. After the pre-ballast is completed, the hull is lifted off the water surface;
4. The gravel is transported from the reclaiming funnel through a stone conveying system to a riprap pipe with a total length of up to 75 m;
5. Through the joint movement of large and small cars, the riprap pipe is moved in the “mouth” shaped moon pool in the middle of the hull to complete the riprap leveling operation;
6. When the riprap leveling and inspection and acceptance work of one position is completed, the hull is lowered, the pile legs are lifted, the riprap boat is moved to the next position, and the riprap leveling operation is repeated;
7. Repeat the completion of the riprap leveling operation of 7 positions to lay the gravel cushion of a standard immersed tunnel.
(Splash diagram of riprap flattening ship)
The above process seems simple, but the technical content contained in it is not small. Moreover, the State Intellectual Property Office and the World Intellectual Property Organization reviewed and decided that the “Deepwater Riprap Flattening Ship” patent won the China Patent Prize in 2015, which is known as “China Intellectual Property Oscar”.
In the end, what are the doorways, and today we will take you to an in-depth interpretation.
(2) How to ensure the stability of the hull when the riprap is leveled?
In order to achieve good riprap leveling accuracy, many key technologies are required. One of the most basic requirements is to ensure the smoothness of the hull under working conditions.
1. Adopting self-lifting structure, the hull is stably inserted into the seabed
"Jinping No. 1" adopts a self-elevating structure. During work, four 90-meter-long legs placed at the four corners of the hull are inserted into the seabed to lift the hull as a whole above sea level to prevent the hull from swaying.
However, simply inserting the bottom of the sea is not enough. This is like inserting a nail into the soil and hitting it with a hammer to make it completely stable.
2. The pre-ballast system will fasten the legs like a hammer.
Similarly, after the legs of “Jinping No. 1” are inserted into the sea floor to lift the platform, the weight caused by the weight of the platform, the variable load, and the load caused by the wind and waves will be added to the pile legs. If the legs inserted into the sea floor are not secure enough, the pile will continue to sink. , affecting the fixed position of the hull, even in the case of poor sea conditions, seabed penetration may occur, with catastrophic consequences.
Therefore, it is very necessary to find an effective "hammer" to fasten it. This hammer is the pre-ballast system on the platform.
The purpose of pre-ballasting is to allow the legs to be inserted deeper into the seabed. To achieve this, the platform can be used in two ballasting modes.
The first type is diagonal ballast: when the four legs are inserted into the seabed and the platform is lifted, the two legs at the corner are locked first, and then the lifting device is used for the other two legs. Stretch to apply a load. When the load reaches a certain level, the leg is locked, and then the other two are loaded, so alternately until the preload is satisfactory. This method is equivalent to the total weight of the hull platform, and the pressure is increased by means of four supports and two supports to achieve ballast.
The other loading method is four-corner balanced ballast. After the four legs are inserted into the soil, the ballast water is pumped into the eight ballast tanks of the platform through four loading pumps arranged on both sides of the ship's side. The total weight of the hull, using the weight of ballast water of nearly 10,000 tons, to achieve balanced ballast. In this ballast mode, it is necessary to ensure that the water inlet speeds of the water tanks are consistent to ensure the balance during the ballasting process.
3, pile leg lifting system: losing a gear can still work normally
As the support of the entire platform, the importance of the legs is self-evident. Not only must the "nails" be deep, but the nails themselves must be strong enough.
The pile leg structure needs to face problems such as large volume, complicated internal structure, high welding requirements, and insufficient welding space.
For this purpose, the leg structure is welded by two steel pipes and back-to-back. The eight legs are used for lifting and driving, and the pile legs are designed as an independent and complete lifting system, which is convenient for overall installation and maintenance.
(Spread of the leg lift system)
In order to further ensure the reliability of the leg lifting system, the failure of the lifting system may be evaluated during design. According to the evaluation results, if the leg is in normal working condition and loading work, if the gear suddenly loses a gear due to the fault, the load of the other 7 gears in the lifting system can still be guaranteed within the maximum load requirement and does not affect the normal operation.
(3) How to accurately rip the stone to level the ship?
The immersed tunnel with a total length of 5664 meters is a segmental design with a total of 33 pipe joints. The standard pipe joint consists of 8 pipe segments, 180 meters long, 37.95 meters wide and 11.4 meters high, with a mass of over 72,000 tons.
(laying pipe section sectional view)
To lay a gravel roadbed for such a pipe joint, it is first necessary to ensure that the riprap pipe that protrudes into the sea has the ability to move in a multi-dimensional space.
For this purpose, the mobile cart and trolley on the platform hold the riprap pipe to move within the “mouth” shape of the horizontal plane, and the follower belt follows the trolley to ensure sufficient supply of gravel material. The lifting winch is responsible for the riprap. Lifting movement.
With the above device, the riprap system can operate normally. However, in order to achieve good riprap accuracy, the head of the 1524 mm diameter riprap pipe is a fixed main pipe and a telescopic balance pipe. The four sets of displacement sensors on the four balance cylinders work together to adjust the expansion and contraction of the balance pipe. Length to meet the accuracy requirements of riprap leveling.
Moreover, two sets of sonar systems are installed in the head of the riprap pipe to detect the height of the submarine trough bed and the laid gravel base. The position of the riprap tube is dynamically adjusted based on the results of the sonar detection.
At the same time, there are two sets of tilt management systems in the platform to detect the inclination angle of the hull and the riprap in real time, and correct it according to the laying requirements.
(4) What else can the riprap ship be able to level?
After the completion of the gravel bed, the immersed tunnel cannot guarantee a completely smooth laying because of the risk of re-covering the bed by the m&d on the seabed.
During the laying of the Hong Kong-Zhuhai-Macao Bridge submarine tunnel, the E22 immersed tube was subjected to large-area bed back siltation due to the influence of the typhoon, which affected subsequent normal construction.
At that time, there were never precedents for high-precision and high-efficiency dredging in the sea and work industry projects at home and abroad for the high-precision and high-efficiency dredging in the case of a water depth of 48 meters.
After the on-site analysis and technical assessment, the best solution is to transform the existing “Jinping No.1” into a riprap leveling ship with dredging function. “Jinping No.1” used the improved dredging function of the technology to complete the high-precision dredging of more than 2,000 square meters of bed in 28 effective working hours, creating a great technological leap in the hydraulic industry.
(The schematic diagram of the dredging system, the red box in the figure)
On the basis of the “Jinping No.1” riprap leveling, a new set of large and small mobile platform and lifting tower was added to place the suction head of the dredging system on the laid bed, and the dredging pump was used to suck in the sludge. And promote it to the platform. The m&d pipe on the mobile truss on the platform is connected to the m&d hose, and finally the sludge is discharged into the sea 1 km away via the m&d hose, eliminating the impact on the seabed laid bed.
The gravel bed is in deep water, the environment is complex, and the visibility is poor. The dredging system can effectively inhale the sludge without destroying the already laid gravel. This requires a series of calculations to accurately control the position and suction of the tip. To this end, it is necessary to obtain the status data of the gravel bed by means of strong light illumination, underwater imaging equipment, sonar multi-beam scanning imaging, etc., to ensure the smooth implementation of dredging work.
Conclusion:
The “Jinping No.1” self-elevating riprap leveling platform is an important equipment for the island tunnel project of the Hong Kong-Zhuhai-Macao Bridge. It is of great significance for the design and construction of a high-precision riprap leveling platform in China's offshore industry.
Compared with the ordinary riprap leveling ship, the platform can complete many operations such as riprap, leveling and dredging at the same time, and has good flatness, which fills the gap in China. The gap in this field has provided effective support for China's construction of world-class sea-crossing bridges and other difficult offshore projects.
As the most recognized label in the world, Made in China is seeking a strategic upgrade. The "Great China Made" column invites industry authorities and experienced players to present the road to innovation in China.
Please submit news to [email protected]. Once the manuscript is published, it will provide a reward of 800 yuan.
--------------------
Edit | Shi Wenhui
Published on 2017-09-07